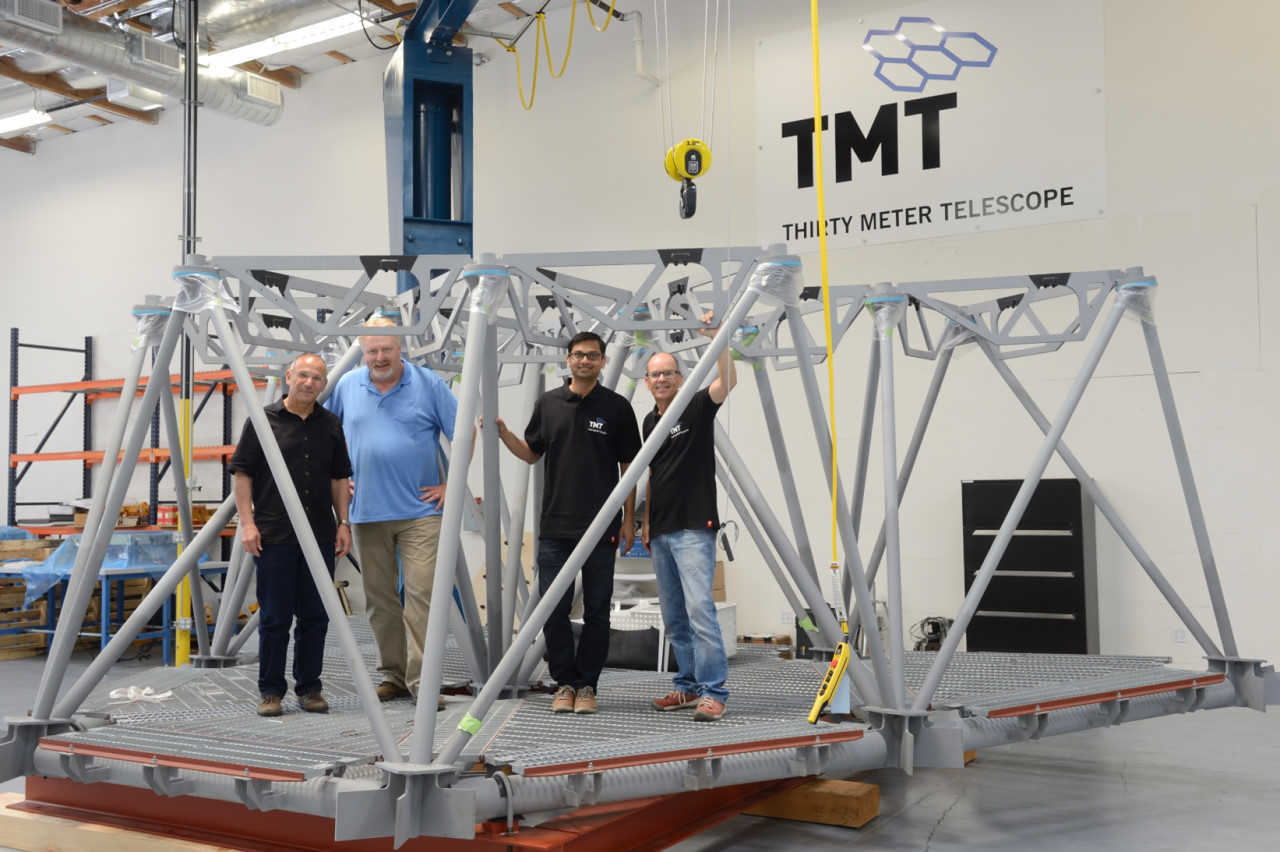
Mirror Cell Prototype arrival at Multi Segment Integration and Test Facility. Left to right: Mark Sirota, Robert Andersen, Vishal Mahulkar, Fred Kamphues
Mirror Cell Prototype arrival at Multi Segment Integration and Test Facility. Left to right: Mark Sirota, Robert Andersen, Vishal Mahulkar, Fred Kamphues
An integral piece of the Thirty Meter Telescope’s Multi Segment Integration and Test facility (MSIT) has just been delivered to California. After leaving the port of Osaka, Japan on March 25, 2017, the Primary Mirror Cell prototype (MCP) arrived at the end of April 2017 and is now undergoing minor modifications prior to its final delivery to the Thirty Meter Telescope (TMT) laboratory in Monrovia. The TMT Primary Mirror System is comprised of 492 active mirror segments; the MSIT will enable integrated testing of up to seven primary mirror segments.
The National Astronomical Observatory of Japan (NAOJ) has contracted with Mitsubishi Electric Company (MELCO) for the design of the Telescope Structure System. Hitachi Zosen Corporation, a major Japanese industrial and engineering corporation, is working with MELCO on its fabrication. Hitachi Zosen built the MCP for MELCO to determine if they can achieve the required dimensional accuracy and validate the proposed welding plan. In December 2016, TMT staff went to Osaka to perform an inspection of the MCP. Hitachi Zosen also designed and built a special container to transport the steel structure as well as a special frame to stabilize the MCP during its long journey to California.
Meanwhile, in California, the concrete foundation for the MSIT was poured at the remodeled TMT Monrovia laboratory, located a few miles from the TMT Project Office. A jib crane is being installed at the laboratory to support the installation and removal of segments into the MSIT. “This is an important step for TMT,” said TMT Laboratory Manager Bob Anderson. “We have poured large foundations, more than four feet deep, to support the MSIT, which weighs over 9000 Kg, and the jib crane.”
The MSIT will be used to verify form, fit and function of all TMT Primary Mirror System components and assemblies prior to full-scale production. In addition, the MSIT will verify the operation and performance of the M1 Control System (M1CS). The M1CS is responsible for turning the 492 TMT mirrors segments into the equivalent of a 30-meter diameter monolithic mirror. The M1CS must measure and control with nanometer precision to be successful. In addition, the MSIT has the ability to tilt the MCP – with seven segments installed – to 15 degrees, which is the tilt of the primary mirror at its perimeter when the telescope is pointing to the zenith. This allows the development team to work through the ergonomic challenges of working at the perimeter of the mirror cell.
“The MSIT demonstrates the international aspect of TMT with contributions from Japan, India and the U.S.,” says Mark Sirota, manager of the Telescope Controls Group. “Tests will be carefully incremented as mirror segments are installed. The full scope of form, fit, and functionality will be verified. Initially we will start with a single segment to confirm the mechanical interfaces between SSA and the MCP. As we begin to install more segments we will continue to focus on mechanical interfaces and over time start to exercise the control aspects of the M1CS. The process will be very systematic, building up capability with time.
“The MSIT will also provide an opportunity to understand the ergonomics of working in the mirror cell. We will be able to exercise our envisioned processes for removing and installing segments, replacing actuators, working at the perimeter of the mirror cell at a 15-degree angle, installing and replacing electronics and cables, and much more. We will be able to use the MSIT for training and even for troubleshooting problems that are encountered while commissioning the complete telescope. This is very exciting, as we’ve been developing this project for years; we surely will reduce risk by assembling these seven segments before assembling 492 of them.”
TMT Communications and Information Systems Kick-off Meetings
ThoughtWorks Team Gathers at TMT Project Office for Second Inception Meeting