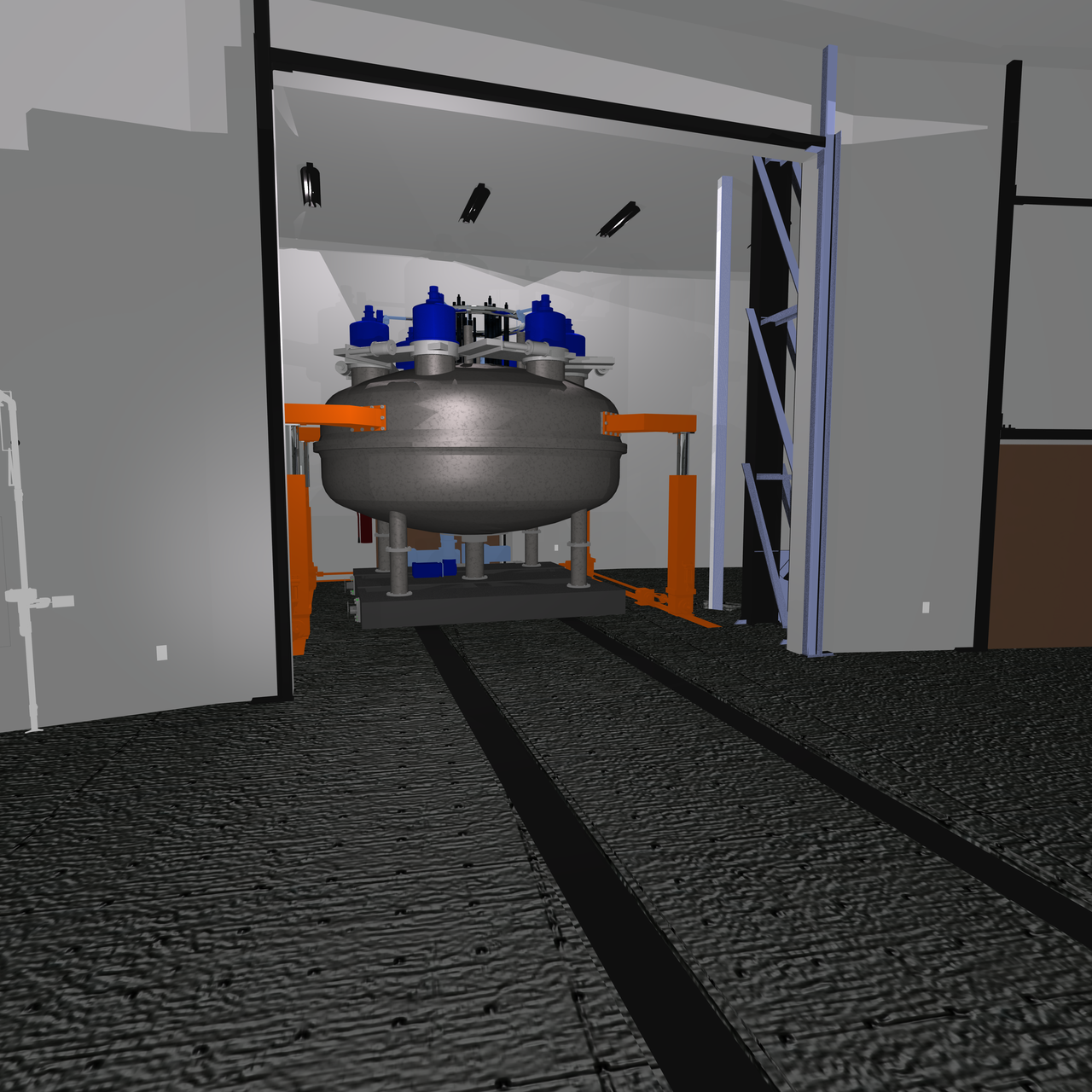
TMT M2M3 Coating Chamber - A rendering of the coating chamber for TMT’s secondary and tertiary mirrors - Image credit: TMT International Observatory
TMT M2M3 Coating Chamber - A rendering of the coating chamber for TMT’s secondary and tertiary mirrors - Image credit: TMT International Observatory
Pasadena, CA – The coating chamber that will provide the required highly reflective thin and uniform coating to both TMT’s Secondary and Tertiary Mirrors (M2 and M3, respectively) recently passed its conceptual design review.
The conceptual design and scope of the Secondary and Tertiary Mirrors Coating Facility (M2M3 COAT) was executed and developed by India TMT Coordination Centre (ITCC), via contract with Hind High Vacuum (HHV) headquartered in Bengaluru, India. The review was to determine the M2M3 COAT facility requirements, design concept and interface requirements with the TMT’s Optics, Controls, Safety, Utility services and Summit facility groups. Experts at India TMT and the TIO Project Office reviewed the operations required to coat M2 and M3, and concluded that the design of the coating process meets TMT’s optical requirements.
“TMT and ITCC started the conceptual design of the future coating facility for M2 and M3 in 2020, in the middle of the Covid-19 pandemic,” said Maheswar Gopinathan, ITCC Work Package Manager at Indian Institute of Astrophysics. “Despite the serious challenges created by the pandemic, the Design Team was able to ramp-up cooperation and efforts in order to present a successful Conceptual Design at the Review on August 3-4, 2021.”
“Congratulations to the M2M3 COAT Design Team including members from TMT Optics, ITCC and HHV for presenting a highly mature design for that stage,” added Fengchuan Liu, TMT Project Manager. “This is the result of a positive and productive collaboration even with meetings held entirely online.”
The coating requirements of the M2 and M3 mirrors are critical to the function and success of the TMT Observatory, as the telescope needs the highest optical reflectivity performances to collect photons from the faintest objects in the Universe.
The coating plant is designed to apply optical coating to the telescope’s M2 and M3 mirrors at first light and during the lifetime of the observatory when M2 and M3 mirrors will require periodic recoating. TMT’s M2 & M3 coating facility ultimately will be installed at the observatory site and will consist of two distinct functional areas: a space dedicated to mirror servicing, where the stripping of the old coating takes place, and a coating chamber area, where the large vacuum chamber and its main components will be located, to apply the new coating.
The chamber has to be large enough to accommodate the variation in size and shape of both the M2 (3.1m diameter, convex) and M3 (elliptical in shape, 2.5x3.5m, flat) mirrors. The deposition system, with a number of magnetrons and targets, will ensure that the layers of coating meet the required high reflectivity, uniformity and durability performance.
The coating plant houses a number of magnetrons and targets that are fully capable of producing a highly reflective thin and uniform silver-based coating on M2 and M3 mirrors with the specified quality - Image credit: TMT International Observatory / HHV
The custom designed coating chamber for TMT will allow precisely controlled depositions of thin and uniform layers of metallic and dielectric materials. It will be conceived to operate in a high vacuum to ensure a pure and durable coating. For that purpose, the coating unit is a large vacuum chamber with a diameter of ~ 4.5 meters. It is divided into two vessel sections and the mirror will be loaded into the lower half of the chamber and laterally secured onto a support system. For the loading and unloading of the mirror, the lower half of the chamber will be mounted on a rail driven by a high precision motor gear system and will be moved from the coating unit location to a mirror handling tool position.
During the coating process, the top part of the chamber will be positioned on top of the lower part in which the mirror will be loaded, and the chamber will sealed. The chamber will then be pumped down to achieve the required vacuum level and the mirror will be rotated continuously beneath the sputter sources to receive its coating.
Magnetron sputtering will be used to deposit a thin uniform silver and protective coating on the mirror. During this process, the magnetrons, located above the mirror at different angular positions of the vacuum chamber, will sputter blocks of ultra-pure silver or other materials for deposition. The TMT selected coating recipe includes silver for reflection as well as additional elements to provide protection and adhesion.
The M2M3 COAT design team presented detailed simulations and models based on different parameters and scenarios; for example, the degassing of the vacuum chamber, or possible remote access for controlling the coating process.
The reflectance data derived from the models are very promising considering the size of the coating unit (chamber diameter larger than 4 m) and the total size of the mirrors (nearly 15 m2) to be coated.
Prototyping will soon begin to hopefully validate the conceptual design of the magnetrons assembly and architecture. Future lab trials will be used to verify the modeling results obtained for the reflectivity and coating thickness. Full validation and fine tuning of the coating process will be done during the later testing phase of the system. A system of safety devices and interlocks will be included in the Mirror Coating System to protect against hazards to personnel, mirror, and equipment.
“The M2M3 COAT team has delivered a clear and technically viable solution due to HHV’s strong heritage in the design and construction of coating chambers operating today for astronomical telescopes,” said Josh Church, Associate Mechanical Systems Engineer at TMT and Chair of the review. “The conceptual design of TMT’s M2 and M3 coating chamber has been well established, and the team is ready to bring the coating chamber to its next development phase.”
HHV has tremendous experience providing coating systems for the astronomical telescopes in
India. Below is a video demonstrating a test that was performed on a mirror coating chamber manufactured by HHV for the 2m Himalayan Chandra Telescope.
Test on previous mirror coating chamber manufactured by HHV (compilation) HHV tested the mirror coating system assembled for the 2m Himalayan Chandra Telescope in the factory of Bengaluru. Later, the chamber was installed at the Indian Astronomical Observatory located in Hanle, at the high altitude of 4500 m. - Video credit: Hind High Vacuum Company
Screenshot participants of the Conceptual Design Review for TMT’s Secondary and Tertiary Mirror Coating Facility on August 4, 2021 - The review panel included professionals from TIO and the India TMT Coordination Center. Nearly 30 engineers and scientists attended the review conducted by video conference - Image credit: TMT International Observatory
Participants of the Conceptual Design Review of TMT’s Secondary and Tertiary Mirror Coating Facility. A group of more than 30 engineers and scientists attended the review held remotely on August 3, 2021 - Image credit: TMT International Observatory
TMT successfully passes a formal milestone review for the planning of its future operations
TMT’s Statement on Astro2020 Decadal Survey