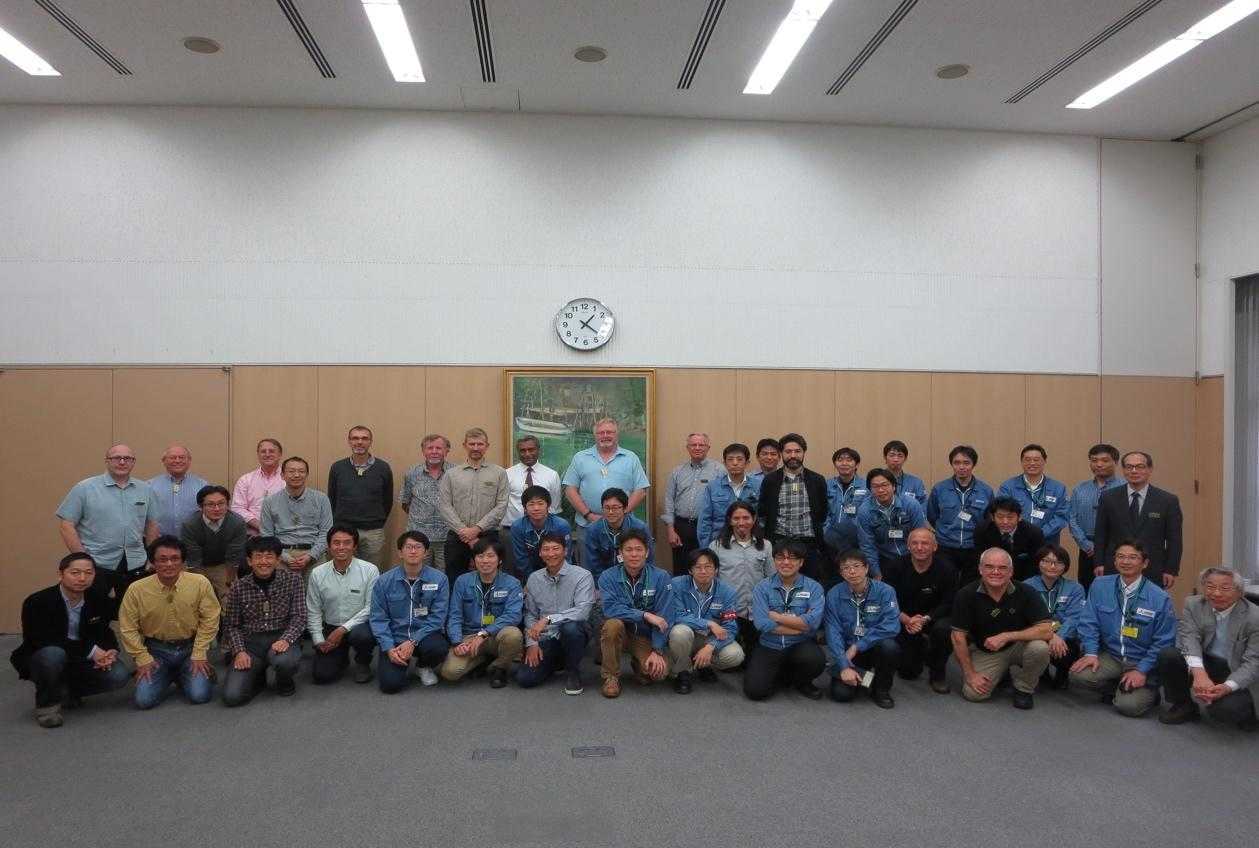
TMT Telescope Structure review meeting participants at MELCO, Japan
In mid-December 2016, an international panel of reviewers met at the Mitsubishi Electric Corporation (MELCO) facility in Amagasaki, Japan, for the last of three final design review presentations for the Thirty Meter Telescope’s (TMT’s) telescope structure. This review focused on the final design of the Telescope’s Segment Handling System (SHS), the Aerial Service Platform (ASP) and the access Elevator. The committee has since concluded that the design of all telescope subsystems is ready to enter its final phase.
The first design review presentation concentrated on the main telescope structural design, while the second focused on the telescope software and control system. An overall Final Design Completion Review (FDR-C) of the entire Telescope Structure will be conducted next. This final review will verify that the key actions from previous reviews have been fully addressed and can be closed. FDR-C will be the major decision point for proceeding to fabrication of the telescope structure.
The review board was chaired by TMT Systems Engineering Group Leader, Scott Roberts. Board members included engineers from TMT and the National Astronomical Observatory of Japan (NAOJ), as well as the Technical Director of Ride Engineering from Walt Disney Company. The design work presented at the review was led by NAOJ, through their subcontractor MELCO.
The scope of the three-day meeting included the review of the complete design, the safe access and all safety aspects for the operation of the SHS, ASP and Elevator systems. The SHS couples a large customized telescope mounted bridge crane with the Segment Lifting Fixture (SLF), which is a precision robotic hand that safely removes, transports and installs the 492 primary mirror segments. It is capable of efficiently orchestrating the complex movements required to safely remove and replace 10 primary mirror segments in one day. To achieve the precision, efficiency and reliability needed for the primary mirror segment exchange, the SHS employs several subsystems: a trolley that supports and moves the SLF, an elaborate hardware and software control system, and a heavy duty lifting system, which deploys and retracts the bridge crane.
The ASP is a dedicated personnel lift mounted to the telescope base. It is used to clean and maintain the secondary and tertiary mirrors. As part of the telescope structure, the ASP must survive the intensity of major earthquakes and utilizes a proven design adapted from Japanese fire trucks.
The Elevator is also part of the telescope structure. It will provide access to all subsystems on the telescope such as the science instruments, the primary mirror cell and the SHS. Like the ASP, the Elevator must withstand strong earthquakes. The Elevator utilizes a sophisticated Seismic Isolation System, which decouples the elevator shaft from its rigid mounts and dampens the oscillations during an earthquake event.
The Structure Telescope consortium includes international engineers from NAOJ (10), MELCO (18), TIO (13) and 1 outside reviewer from both Keck and Disney.
Common Software Design Approved for Production
TMT’S Infrared Imaging Spectrograph IRIS Achieves Milestone